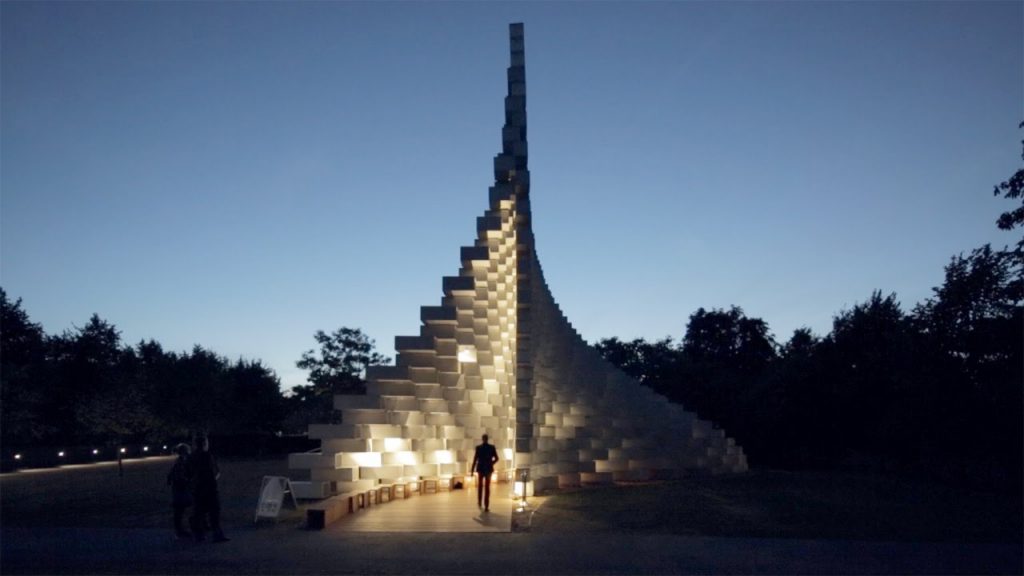
Here we go behind the scenes at the factory where the fibreglass blocks that comprise BIG’s Serpentine Gallery Pavilion were made in this exclusive video produced for material manufacturer Fiberline.
Bjarke Ingels’ firm’s Serpentine Gallery Pavilion opened in London on 10 June 2016, and is a huge undulating structure composed of thousands of fibreglass boxes stacked on top of each other.
BIG’s Rune Hansen, who was project manager for the project, explains that the firm saw the pavilion as an opportunity to test what it is possible to create with its fibreglass material.
“To build a pavilion like this for us as an architecture office is extremely interesting,” he explains in the movie. “It is kind of a lab where we can test materials – the visual aesthetics as well as structural conditions.”
The pavilion, which resembles a wall of bricks that has been “unzipped” to create a void inside, consists of around 1900 hollow fibreglass blocks, which are attached by simple metal connectors.
The blocks themselves are made from sheets of fibreglass of various thicknesses, with heavier blocks at the base and lighter ones making up the upper layers.
“We used three different gauges,” Hansen reveals. “The bottom boxes are 10 millimetres [thick], the middle boxes are six millimetres and the top boxes are three millimetres. It’s a lightweight material, but at the same time it’s strong.”
The fibreglass boxes were manufactured at the Middelfart factory of Danish company Fiberline Composites, which more commonly produces composite structural profiles for use in bridges or wind turbine blades.
Our Recommended Books
BIG used a product called Lay Light for the pavilion, which is a translucent material consisting of glass fibres impregnated with a polyester resin.
“All the boxes for this year’s Serpentine Gallery Pavilion were made out of Lay Light material and assembled in our factory in the centre of Denmark,” says Fiberline vice president Stig Krogh Pedersen. “The material is as strong as steel, but only has about one fifth of the weight.”
The material is produced by a technique called pultrusion, in which thousands of strands of glass fibre are pulled through a mould and impregnated with resin.
“We have a production line that grabs the fibres and pulls them through a die, Pedersen explains. “That way we have a continuous process to make profiles as long as we like.”
Fiberline’s factory is clad with the material.
“We used our factory as a kind of prototype,” Pedersen says. “We’ve got a lot of experience with the Lay Light material by doing this prototype of 23,000-square-metres.”
BIG is also using the material to clad its soon-to-be-completed Transitlager project, a conversion of a warehouse in Basel into offices, apartments and galleries.
“The Serpentine Gallery Pavilion is a temporary structure,” Hansen says. “But BIG is also designing a permanent structure using Lay Light to cover 6,000 square metres of the building.”
Hansen says that as well as its strength, the translucency of the material makes it interesting for architects.
“When you go close to it you will recognise the details, you’ll see the actual components of the fibreglass,” he explains.
“At night, the pavilion starts to glow because of this translucency. It’s very beautiful.”
BIG’s structure marks the 16th edition of the annual Serpentine Gallery programme, which offers architects the chance to create their first built structure in the UK. The pavilion is open until 10 October 2016 at Kensington Gardens in London’s Hyde Park.